A Ball Mill Grinding Machine is a key piece of equipment used in industries such as mining, cement production, chemical processing, and materials science for grinding materials into fine powders. It operates on the principle of impact and attrition, where balls (typically made of steel, ceramic, or other materials) are used to grind and pulverize materials inside a rotating cylindrical chamber.
---
●How Does a Ball Mill Work?
1. Material Loading:
- The material to be ground (e.g., ores, minerals, chemicals) is fed into the ball mill along with grinding media (balls).
2. Rotation:
- The cylindrical chamber rotates at a specific speed, causing the balls and material to rise and fall due to centrifugal force.
3. Grinding Process:
- As the balls fall back onto the material, they crush and grind it into finer particles through impact and abrasion.
4. Discharge:
- Once the material is sufficiently ground, it is discharged from the mill, either continuously or batch-wise, depending on the design.
---
Roll Ball Mill
●Key Components of a Ball Mill
1. Cylindrical Drum:
- The main body of the machine where the grinding occurs.
- Made of durable materials like steel or rubber-lined for corrosion resistance.
2. Grinding Media (Balls):
- Typically made of steel, ceramic, or other hard materials.
- The size and type of balls depend on the application and desired particle size.
3. Feed System:
- Mechanism for introducing raw material into the mill.
4. Discharge System:
- Mechanism for removing ground material from the mill.
5. Drive System:
- Provides rotational motion to the drum, usually powered by an electric motor.
6. Lining:
- Protects the inner surface of the drum from wear and tear caused by the grinding process.
---
●Types of Ball Mills
1. Overflow Ball Mill:
- Material is retained in the mill until it reaches a certain fineness before being discharged.
2. Grate Discharge Ball Mill:
- Uses a grate at the discharge end to control the size of the ground material.
3. Planetary Ball Mill:
- Used for high-energy grinding, where multiple smaller mills rotate around a central axis.
4. Horizontal Ball Mill:
- A standard design where the drum rotates horizontally.
5. Vertical Ball Mill:
- Less common but used in specific applications like cement production.
---
●Applications of Ball Mills
1. Mining Industry:
- Grinding ores and minerals for further processing.
2. Cement Production:
- Grinding clinker and other raw materials into fine cement powder.
3. Chemical Industry:
- Producing fine powders for chemical reactions or formulations.
4. Ceramics and Glass:
- Preparing raw materials for ceramics and glass manufacturing.
5. Pharmaceuticals:
- Grinding active pharmaceutical ingredients (APIs) into uniform particle sizes.
6. Metallurgy:
- Processing metal powders for sintering or alloy production.
---
●Advantages of Ball Mills
1. Versatility:
- Can handle a wide range of materials and achieve various particle sizes.
2. Durability:
- Built to withstand heavy-duty operations over long periods.
3. Consistency:
- Produces uniformly sized particles.
4. Scalability:
- Available in small laboratory-scale models to large industrial-scale machines.
---
●Disadvantages of Ball Mills
1. Energy Consumption:
- Requires significant energy to operate, especially for large-scale applications.
2. Noise:
- Generates high noise levels during operation.
3. Maintenance:
- Requires regular maintenance to replace worn-out components like liners and balls.
4. Wear and Contamination:
- The grinding media can introduce contamination if not carefully selected.
---
●Factors Affecting Ball Mill Performance
1. Ball Size and Distribution:
- Larger balls are used for coarse grinding, while smaller balls are used for finer grinding.
2. Rotation Speed:
- Optimal speed ensures efficient grinding without excessive wear.
3. Material Feed Rate:
- Too much or too little feed can affect grinding efficiency.
4. Grinding Time:
- Longer grinding times produce finer particles but increase energy consumption.
5. Moisture Content:
- Wet grinding may require additional considerations to prevent caking or agglomeration.
---
●Improvements and Innovations
1. High-Energy Ball Mills:
- Designed for ultra-fine grinding and nano-material production.
2. Automated Control Systems:
- Modern ball mills often come equipped with sensors and automation to optimize performance and reduce operator intervention.
3. Eco-Friendly Designs:
- Efforts are being made to reduce energy consumption and noise pollution.
---
●Conclusion
The ball mill grinding machine is an essential tool in many industries for reducing materials to fine powders. Its versatility, durability, and ability to handle a wide range of materials make it indispensable in processes requiring precise particle size control. However, advancements in technology continue to enhance its efficiency and reduce its environmental impact, ensuring its relevance in modern industrial applications.
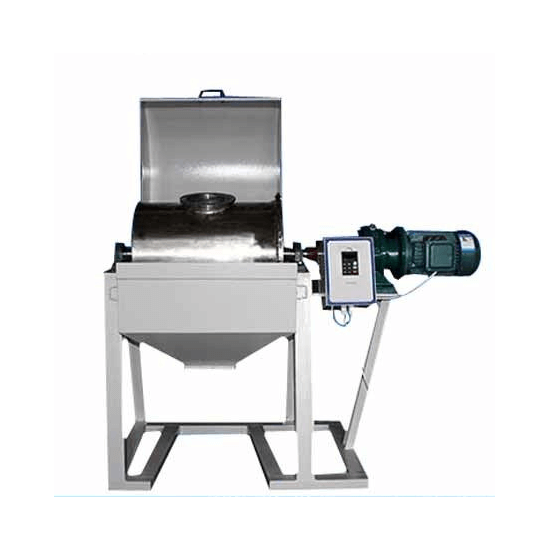