Bar Coater: Precision Tool for Uniform Film Coating
A bar coater, also known as a wire wound bar or rod coater, is a versatile tool used for applying uniform films of liquids, pastes, or slurries onto substrates. It is widely employed in industries such as batteries, solar cells, coatings, and printing, where consistent layer thickness is critical for product performance.
This article explores the design, applications, advantages, and key considerations for using bar coaters effectively.
What is a Bar Coater?
A bar coater consists of a cylindrical metal rod with a tightly wound wire or a smooth surface. It works by dragging the bar across a substrate while spreading the liquid material to achieve a uniform thickness. The thickness of the coated layer is primarily determined by the diameter of the wire or the rod itself.
How Does a Vacuum coating machine Work?
1. Material Application: The coating material (e.g., slurry, adhesive, or paint) is deposited onto the substrate.
2. Rod Movement: The bar is drawn across the substrate either manually or with a motorized system.
3. Layer Formation: The liquid material is spread evenly, and the excess is removed, leaving a controlled film thickness.
4. Drying or Curing: The coated substrate undergoes drying or curing to stabilize the film.
Types of Bar Coaters
1. Wire Wound Bars
- Description: A rod with a tightly wound wire. The wire diameter determines the coating thickness.
- Applications: Common for thin films and precise coatings.
2. Smooth Bars
- Description: A rod without wire, used for thicker coatings or when a smoother finish is required.
- Applications: Suitable for viscous materials.
3. Custom Bars
- Description: Bars designed with specific patterns or grooves to create unique coating effects.
- Applications: For specialized industrial applications.
Key Applications of Bar Coaters
1. Battery Electrode Coating
- Used in lithium-ion batteries and supercapacitors to coat active materials onto current collectors (e.g., aluminum or copper foil).
2. Solar Cell Manufacturing
- Applies films of perovskite, polymer, or other photovoltaic materials onto substrates.
3. Printing and Graphics
- Creates uniform ink or adhesive layers in high-precision printing processes.
4. Adhesive and Paint Coating
- Ensures consistent application of adhesives or paints for industrial and consumer products.
5. Laboratory Research
- Common in research labs to prepare thin films for testing and prototyping.
Advantages of Using a Bar Coater
1. Uniform Coating
- Ensures consistent layer thickness, which is critical for performance-sensitive applications.
2. Ease of Use
- Simple setup and operation, suitable for both manual and automated systems.
3. Cost-Effectiveness
- Compared to advanced coating machines, bar coaters are inexpensive yet highly effective for small-scale and experimental work.
4. Versatility
- Compatible with various materials, substrates, and industries.
5. Scalability
- Ideal for small-scale lab experiments and pilot production lines.
Factors to Consider When Choosing a Bar Coater
1. Wire Diameter
- Determines the thickness of the coating. Choose based on the desired film thickness.
2. Material Compatibility
- Ensure the bar material (e.g., stainless steel) is resistant to the chemicals used.
3. Substrate Type
- Consider the surface properties of the substrate for optimal adhesion and spreading.
4. Application Method
- Manual or motorized operation depends on precision and production scale requirements.
5. Cleaning and Maintenance
- Easy-to-clean designs reduce downtime and extend the coater's lifespan.
Challenges in Using Bar Coaters
1. Limited Control for Complex Patterns
- Bar coaters are less suitable for non-uniform or highly intricate patterns.
2. Thickness Variability with High Viscosity Materials
- May require adjustment or alternative techniques for very thick or uneven liquids.
3. Scaling to Large Production
- Not ideal for high-volume industrial coating processes where advanced machines offer better efficiency.
Conclusion
A bar coater is an indispensable tool for achieving precision and uniformity in thin film applications. Its simplicity, versatility, and cost-effectiveness make it a popular choice in industries ranging from battery manufacturing to solar cells and adhesive coating. Whether in a lab or a pilot production line, a bar coater offers an efficient way to produce high-quality coatings with minimal effort.
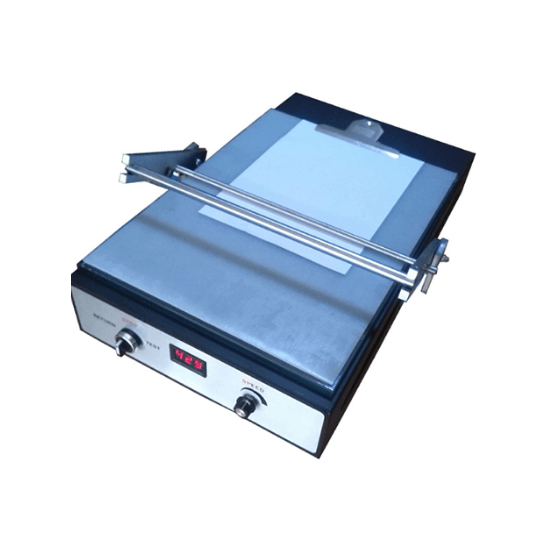